Rev9 (2023) Projects (In Progress)
Rev9 Powertrain System Overview
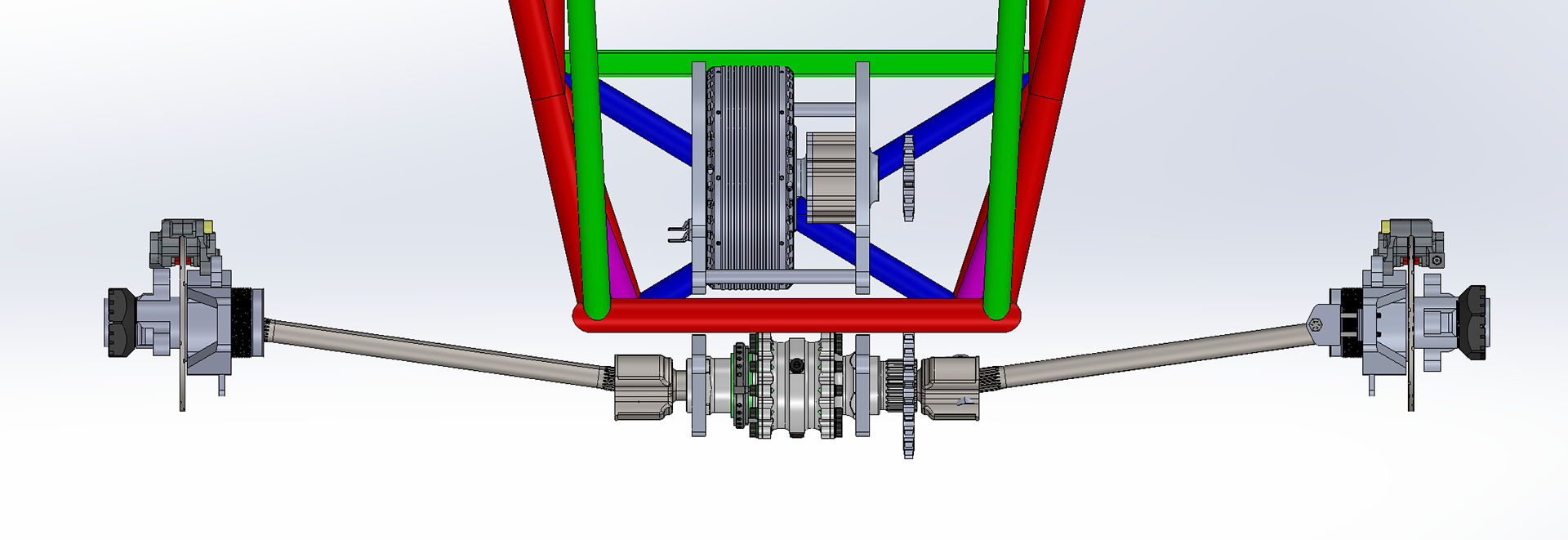
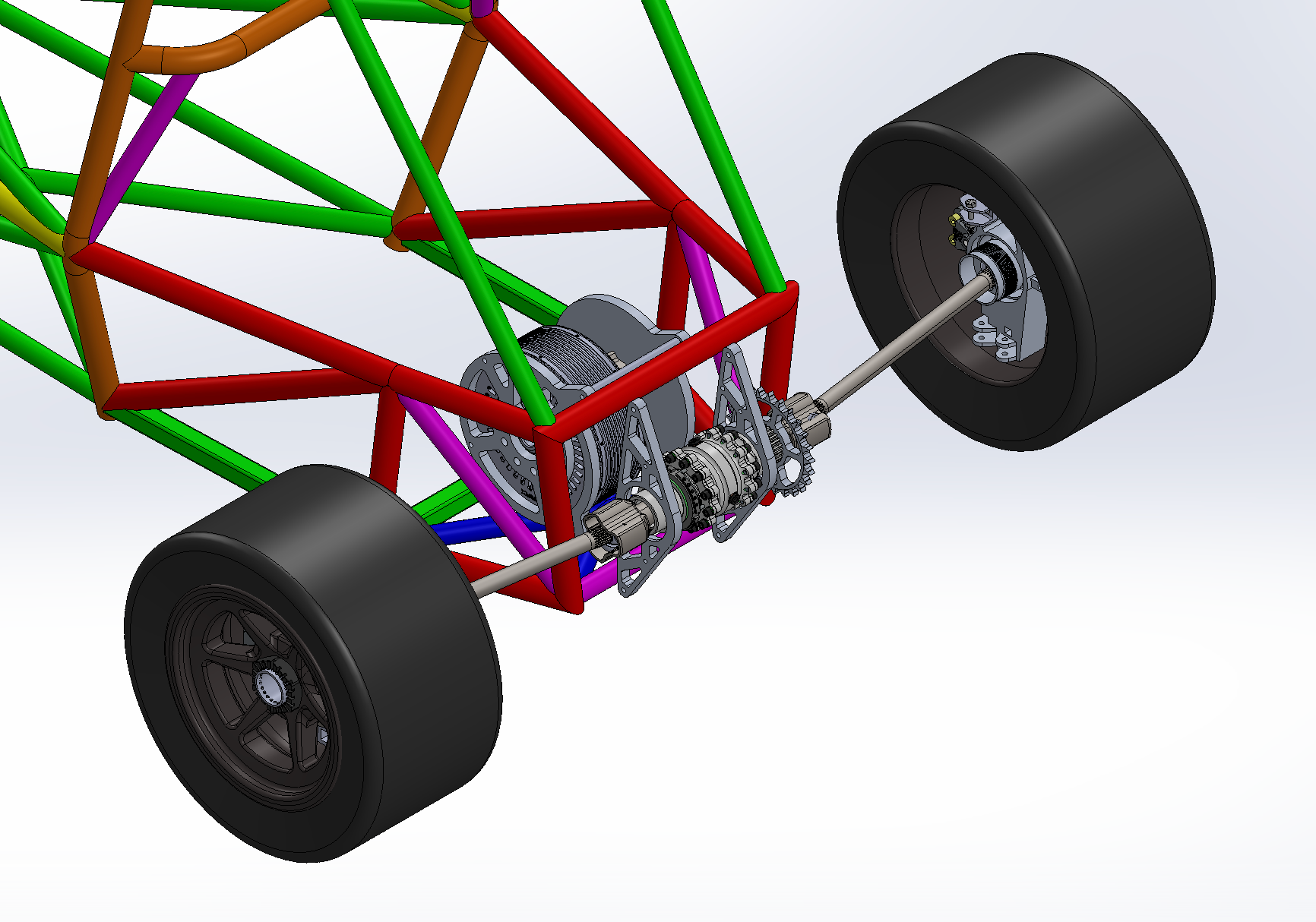
In-progress Powertrain Subsystem CAD
The Rev9 powertrain architecture is very unique; it consists of an Emrax 208 HV motor, a planetary gearbox and a chain-and-sprocket in series, a Drexler limited-slip differential, and custom designed/machined uprights and wheelhubs. The transmission concept being using is very beneficial due to how ratio-dense the planetary gearbox is. This allows us to achieve a higher gear ratio with less overall package volume. This means we can downsize our motor from the previous year's vehicle while minimizing our sprocket size and, in turn, our package length. It also enables us to move our differential outside the chassis so that the chassis could shorten, reducing our chassis weight by around 5 lbs (~7%). The overall powertrain system mass is expected to be 10 lbs lighter than the previous year (a 12% reduction).
Rev9 Planetary Gearbox Design
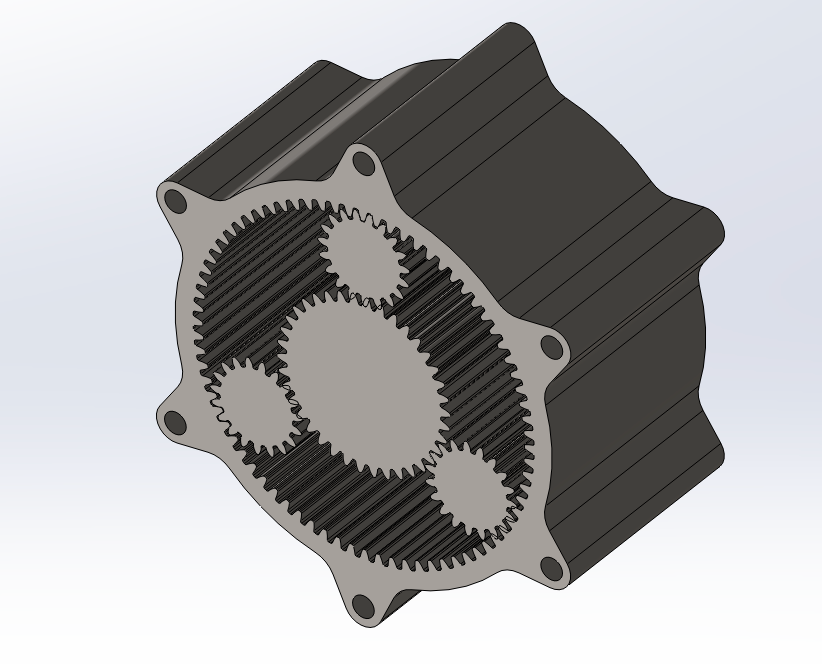
In progress gear CAD
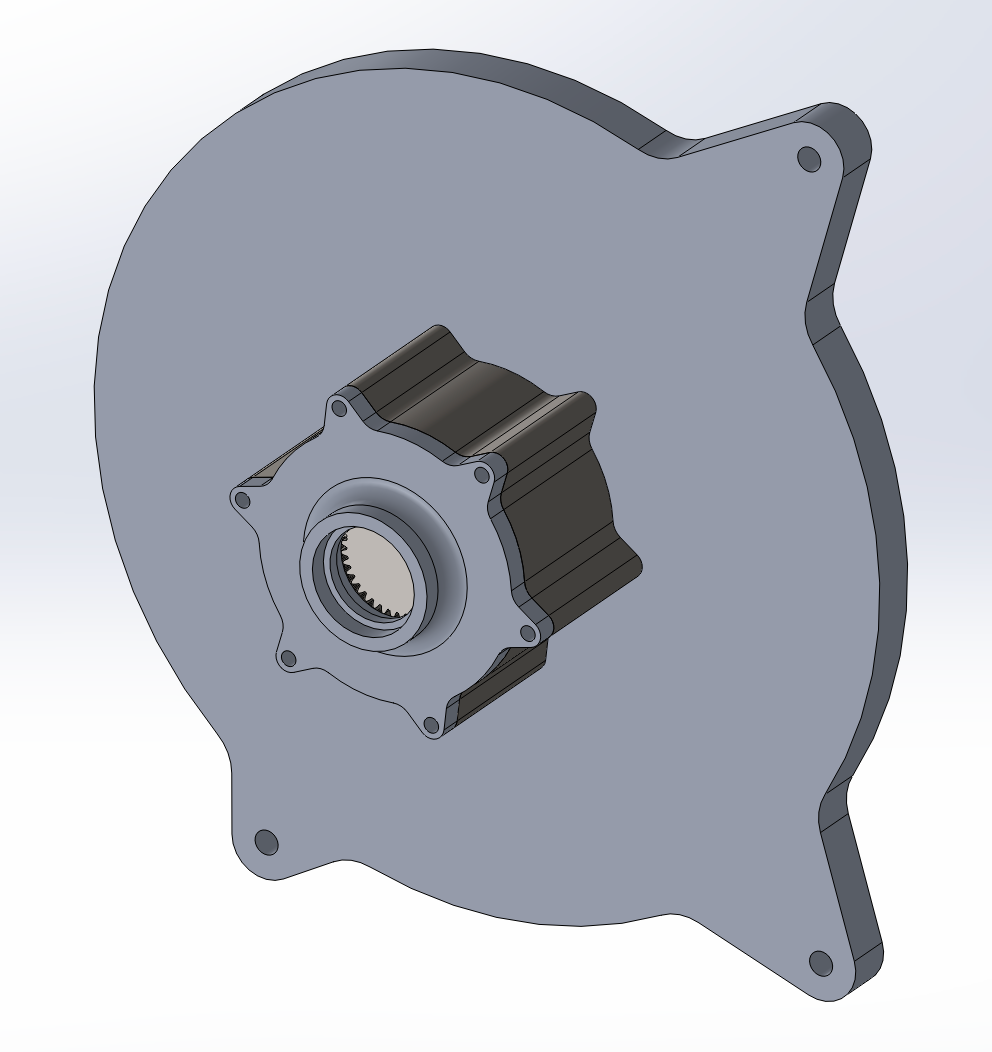
Entire gearbox package
This planetary gearbox has a ratio of 3.5:1. It consists of a sun gear, three planets, and a ring gear; the rotation scheme is fixed ring with carrier rotation. The gears are all made of 4140 prehard steel and are machined by a team sponsor. I designed the backside plate to be very large so that it can be tabbed directly to the chassis and the gearbox can be fastened directly to it, allowing the plate to mirror the motor mounting plate and ensure parallelism and concentricity between the motor output shaft and the gearbox.
*This CAD is still in progress!
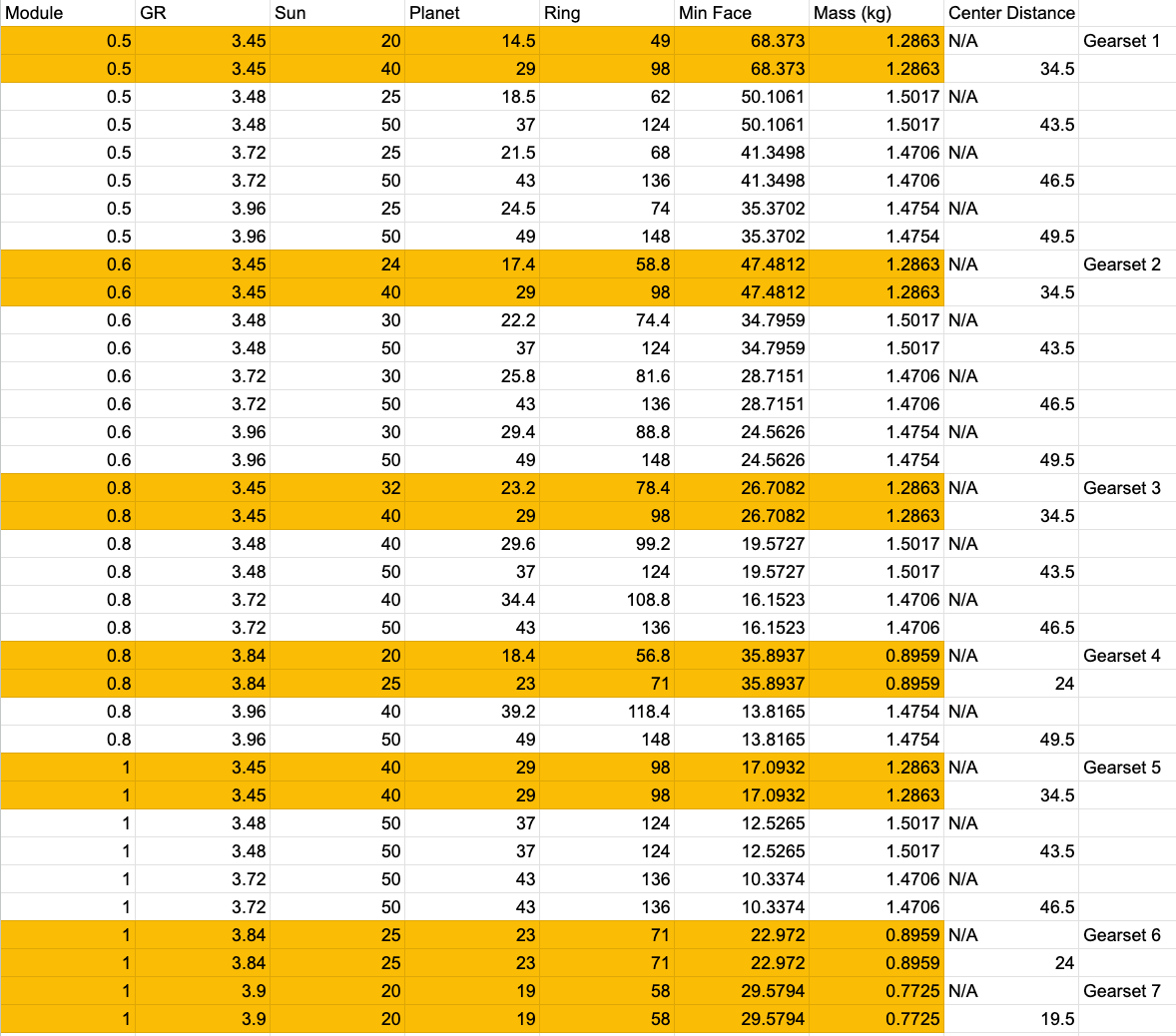
The gear macrogeometry (face/width, tooth counts, pitches, etc.) was determined via a custom-built Python script. It takes in motor torque, gear material choices, safety factors, and a target gear ratio. The script then sweeps across a range of modules and gear ratios to find a gear combination that works for the required loading. It considers torsion on the gear bodies, bearing failure on the interior bores of the planets, and shearing of the planet pins. It outputs a CSV of all possible tooth counts within the given gear ratio range that satisfy the hunting ratio (GCD of all meshing gears is 1), which minimizes tooth wear by ensuring that each tooth on one gear meshes with every tooth on the other gear before returning to the initial tooth in contact. Gear microgeometry (tooth profiles) is currently being determined via KISSsoft, a gear-specific CAE software.
Rev9 Cooling Radiator Performance Sim
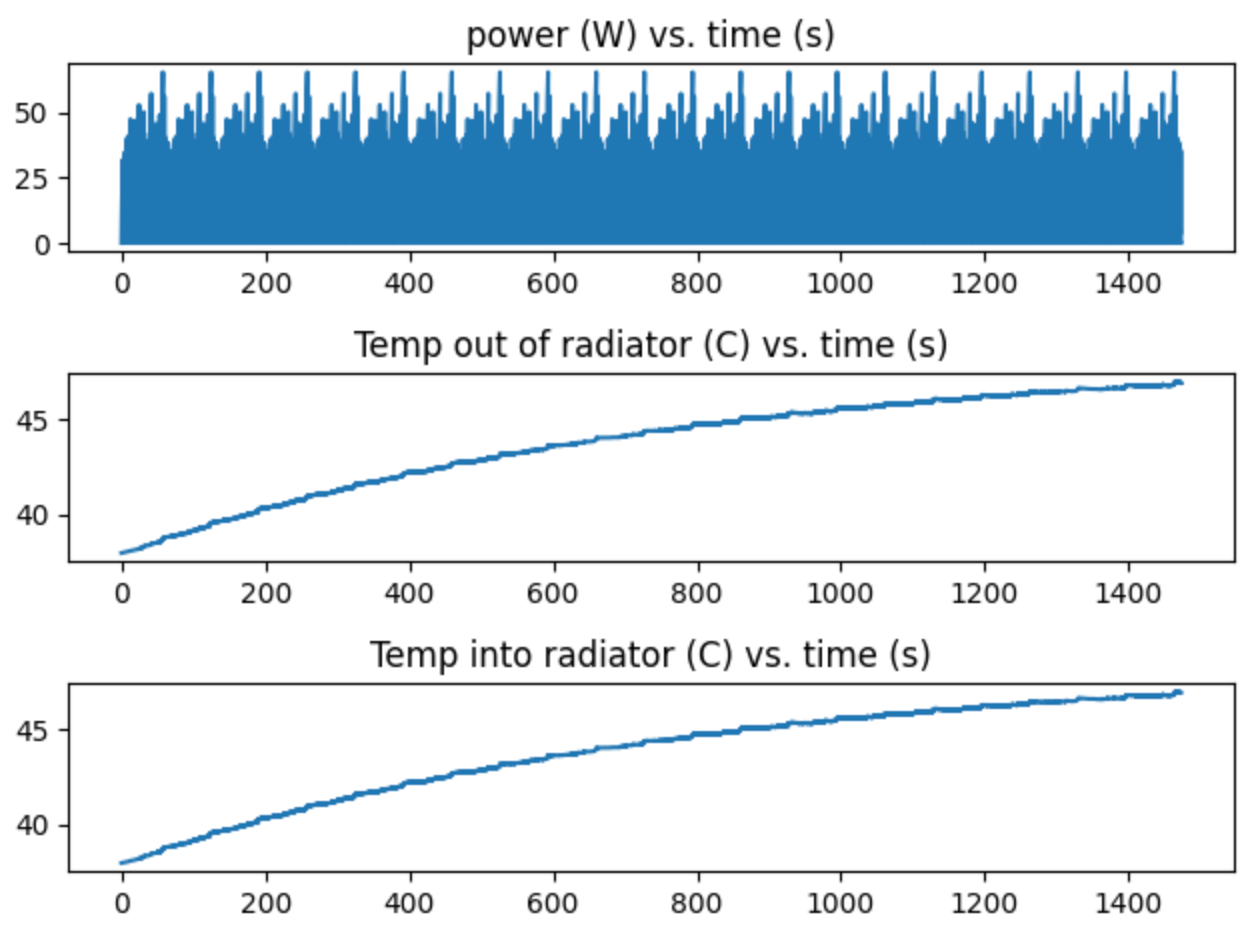
Output graphs from sim depicting motor power and expected coolant temperature into/out of the radiator over the course of the endurance event
The cooling sim was coded in Python. It takes in things like radiator and fan characteristics, ambient temperatures, required flow rate for our motor, and even a motor efficiency chart. It runs through output motor data from our team's lap sim to determine exactly how much power the motor is using throughout the endurance event (a 22 km timed race). It calculates the expected heat dissipation through the radiator at each time step using the NTU-effectiveness method. It keeps track of coolant temperature over the course of the 22 km to ensure the maximum coolant temperature is less than 50 C, which is the maximum allowable coolant temperature into the motor, as given by our motor's manufacturer.
Rev8 (2022) Uprights
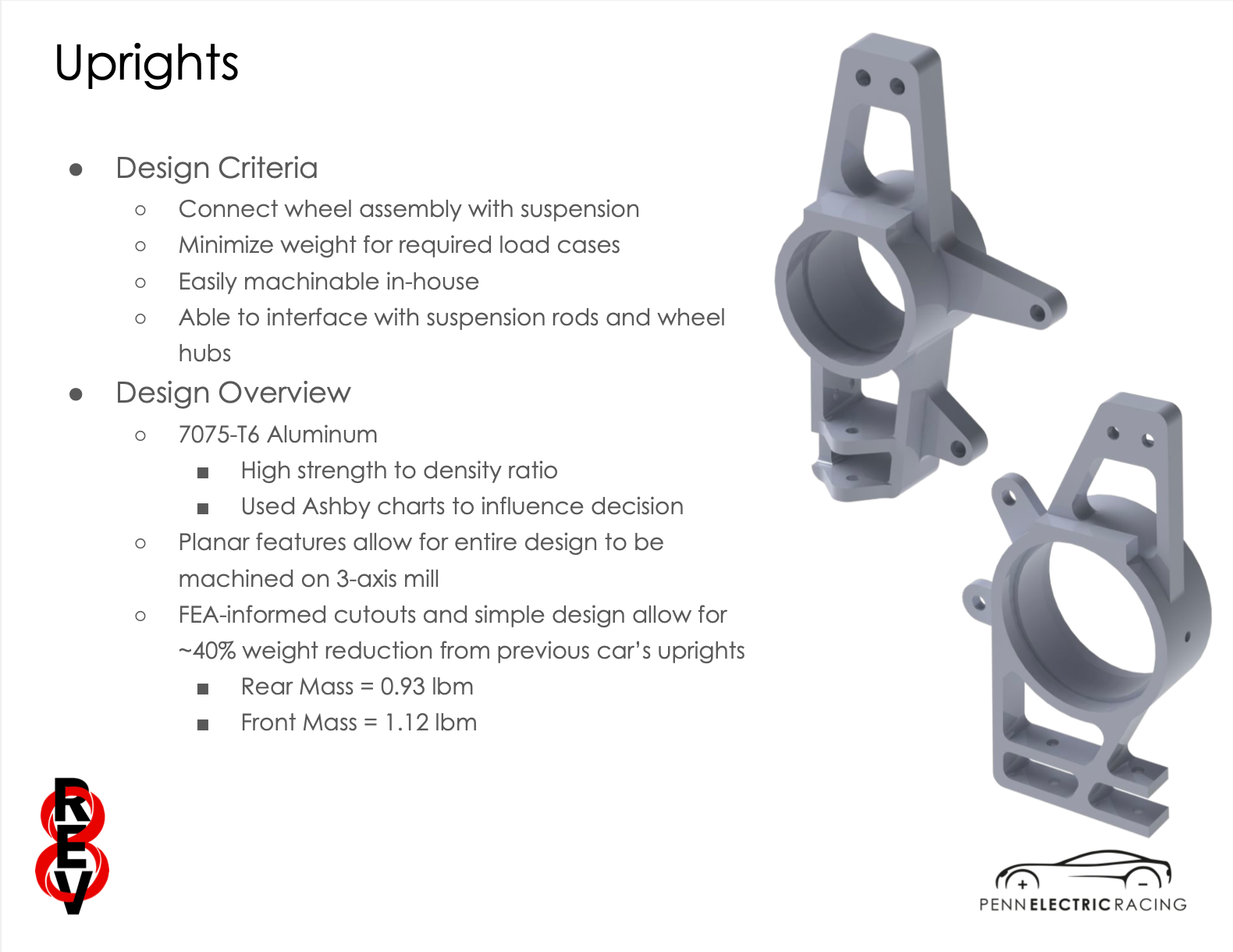
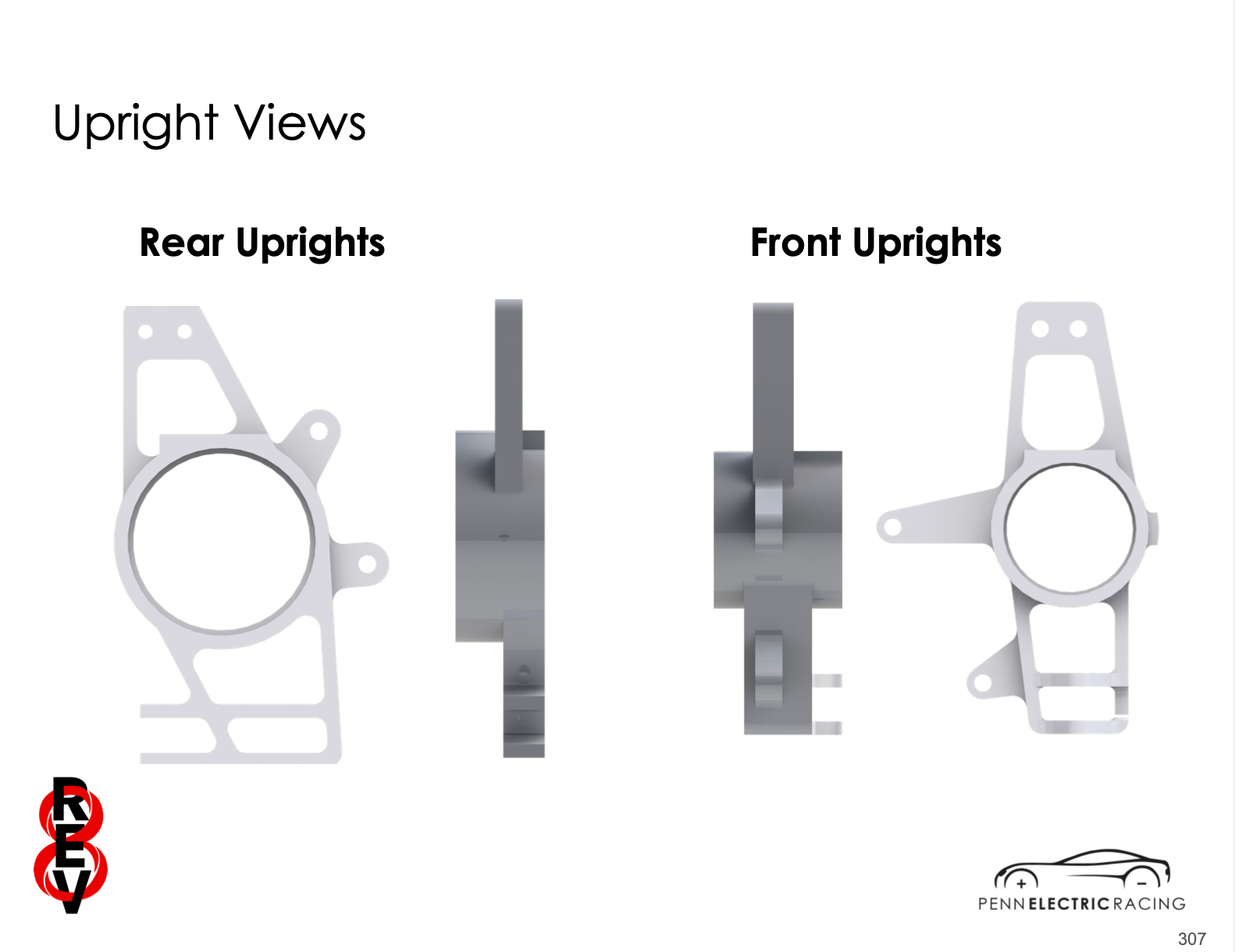
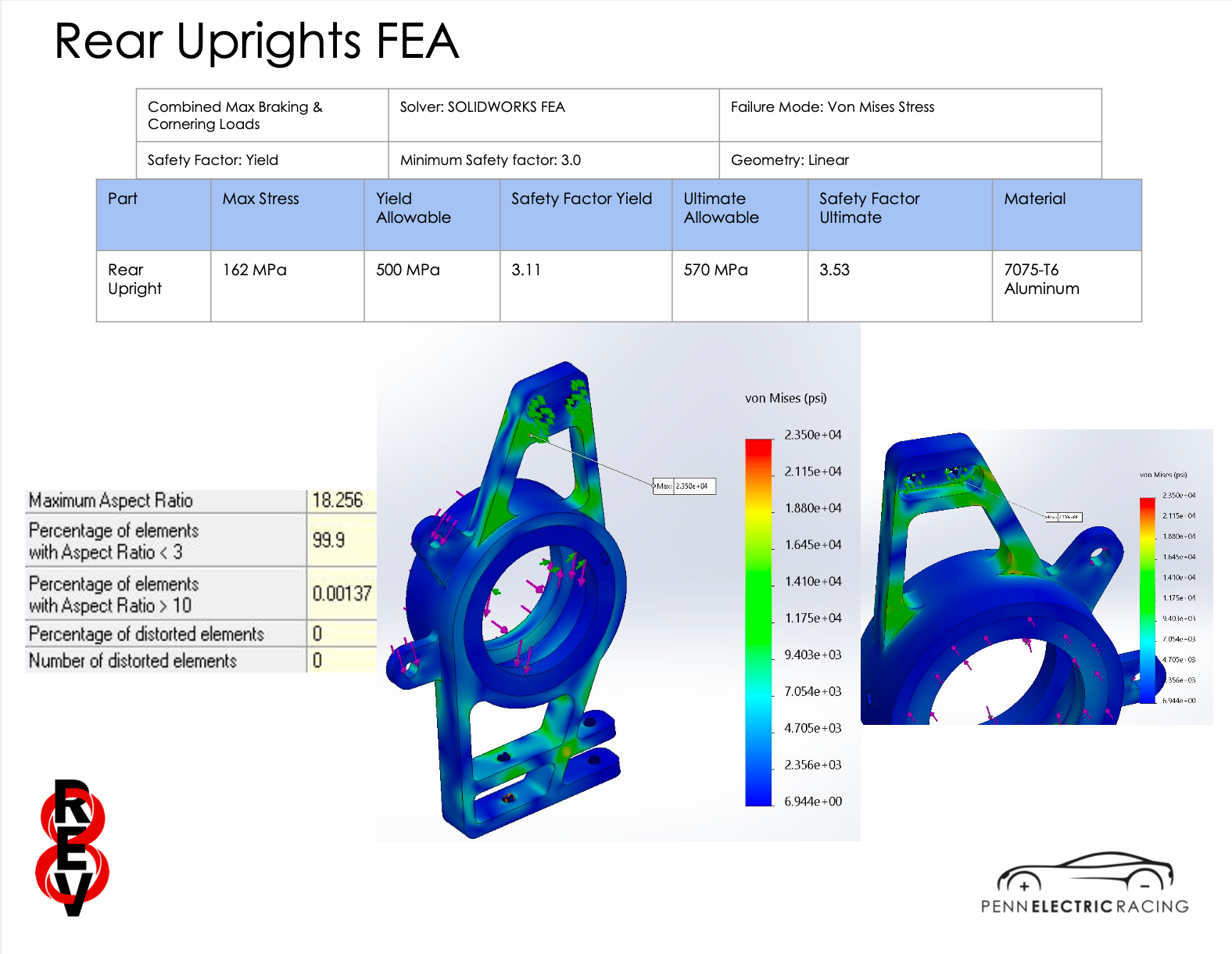
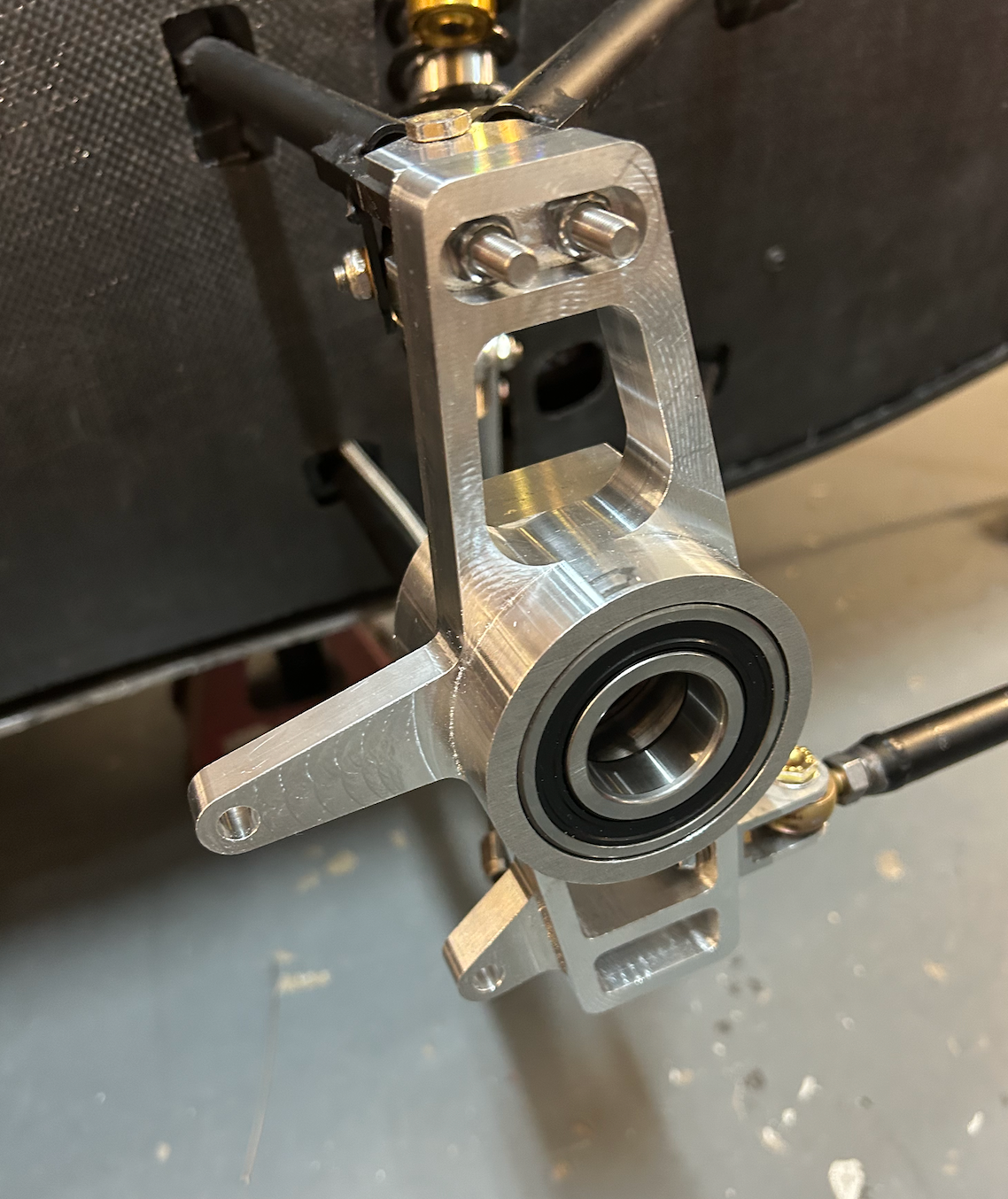
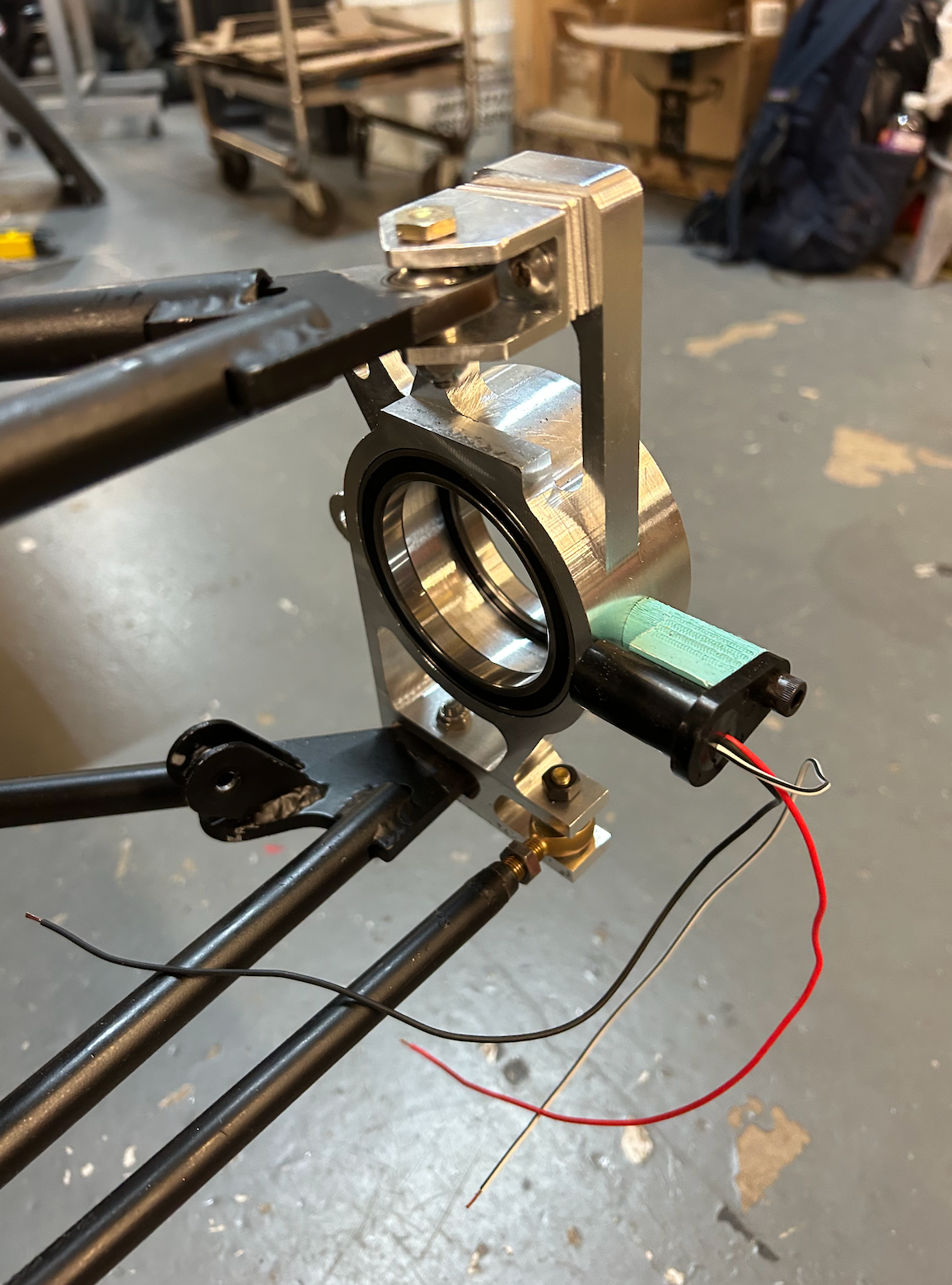
I designed the uprights (or knuckles) for PER's 2022 vehicle, Rev8. My main priorities in design were manufacturability and mass reduction. I achieved the former by making nearly all features 2D and planar to ensure excellent precision/tolerances with our in-house mills. The overall combined mass of the four uprights was ~4.1 lbm, which is a reduction of around 40% from the previous year's design. All CAD was done in SolidWorks. The CAM for machining was done in MasterCAM and the part was machined with a 4-axis Fadal mill.
Machining a rear upright on 4-axis mill
Rev7 (2021) Projects
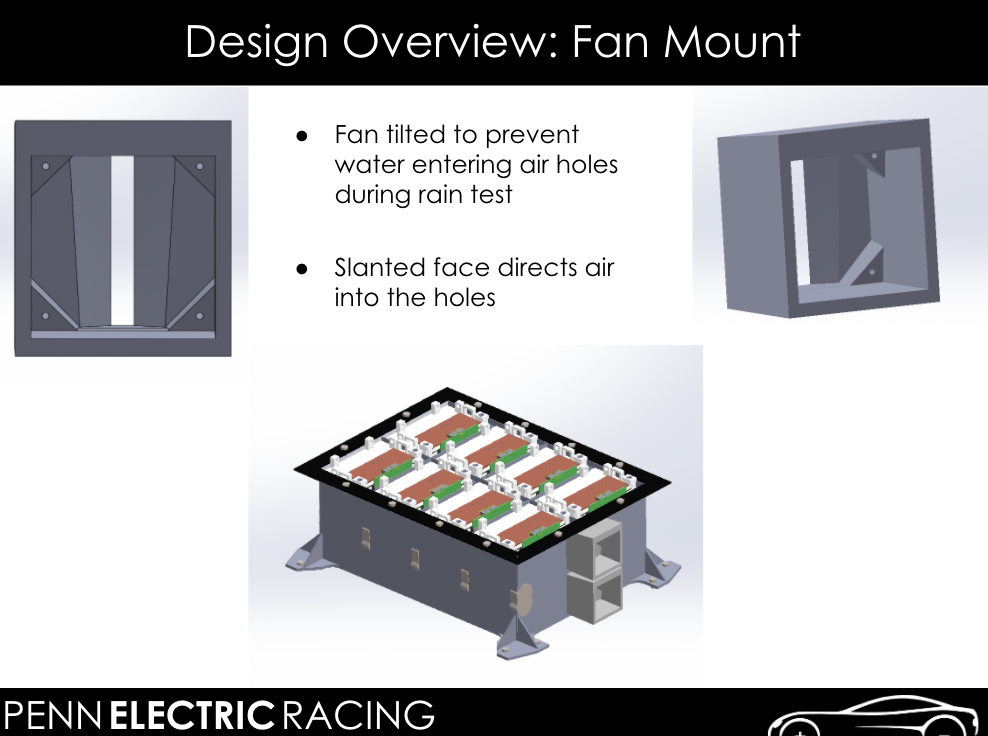
Rev7 Backup Accumulator Fan Mounts
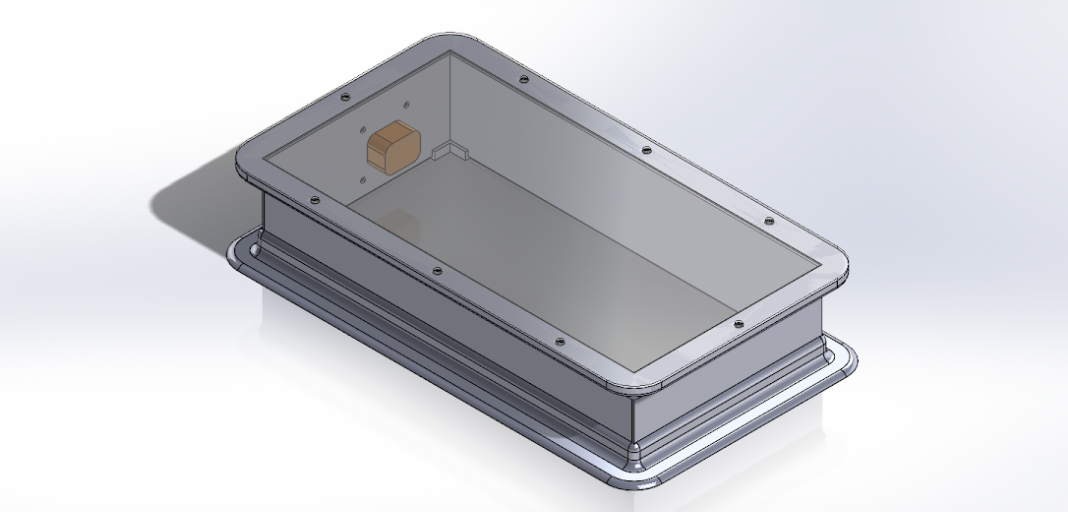
Rev7 Backup Accumulator Penthouse
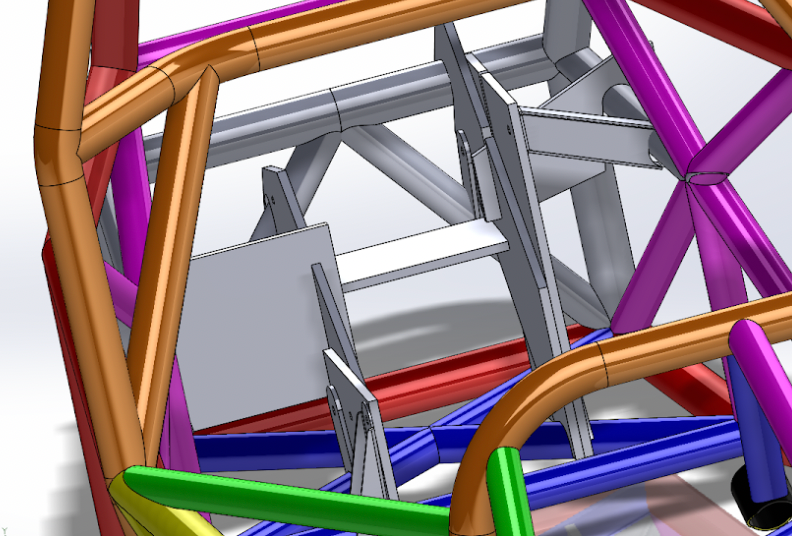
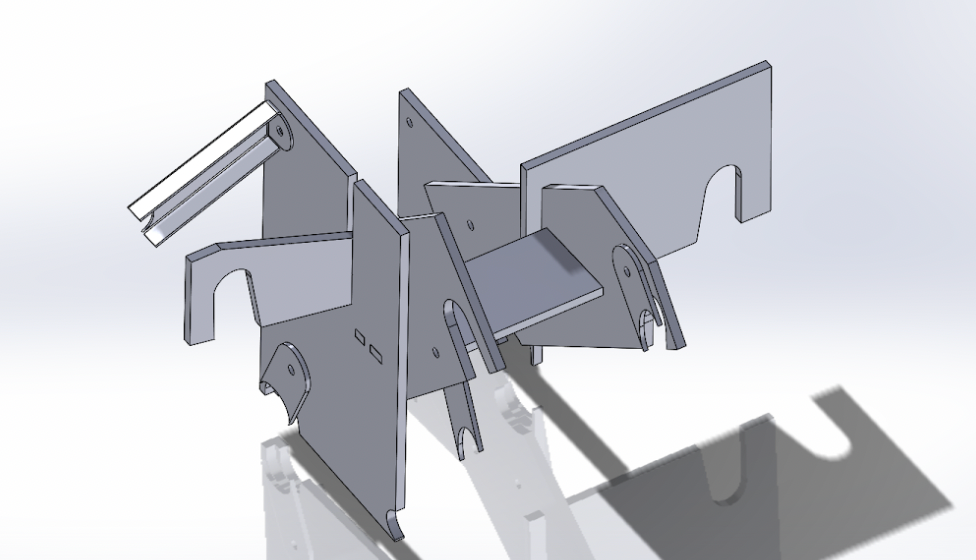
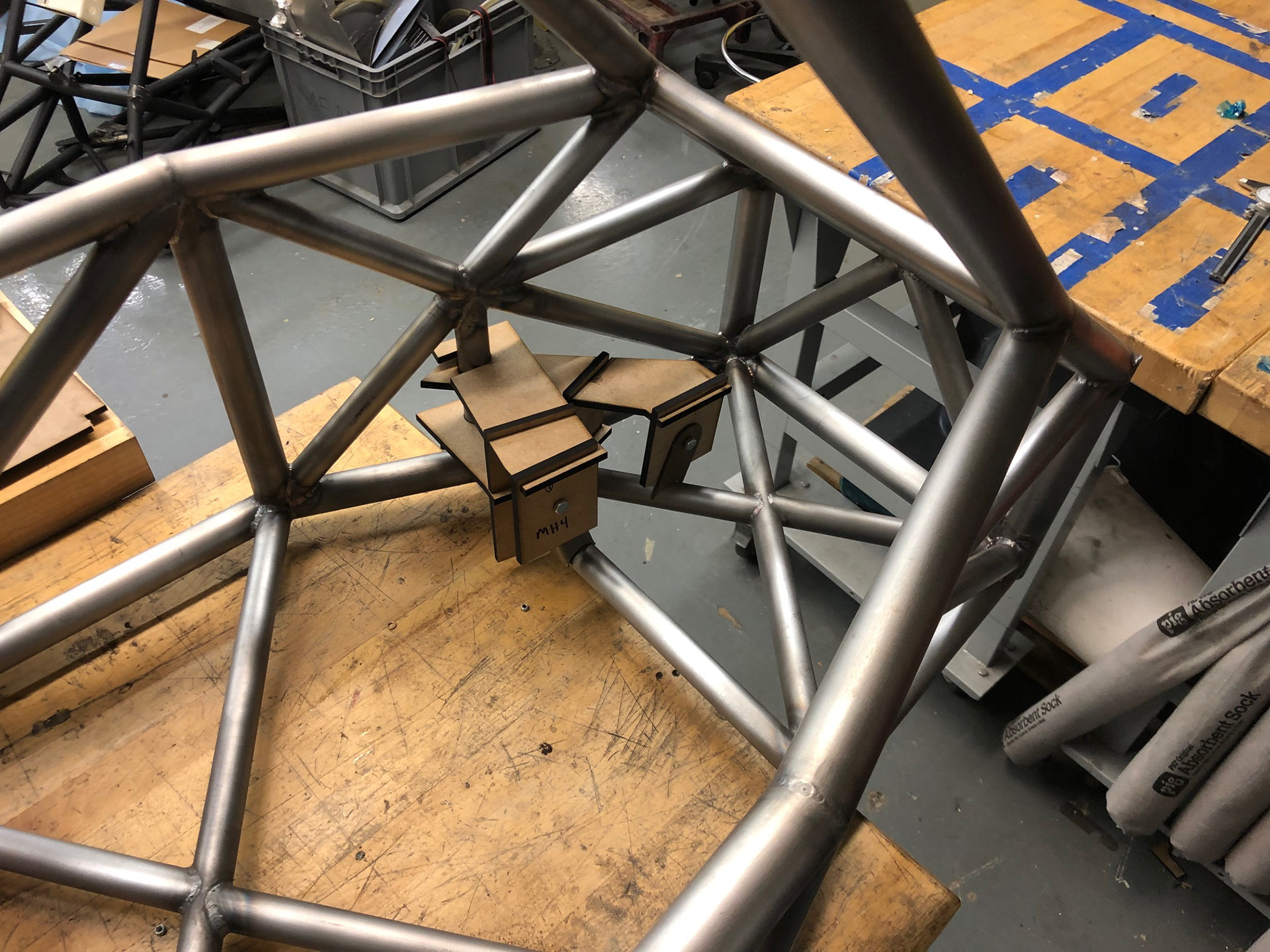